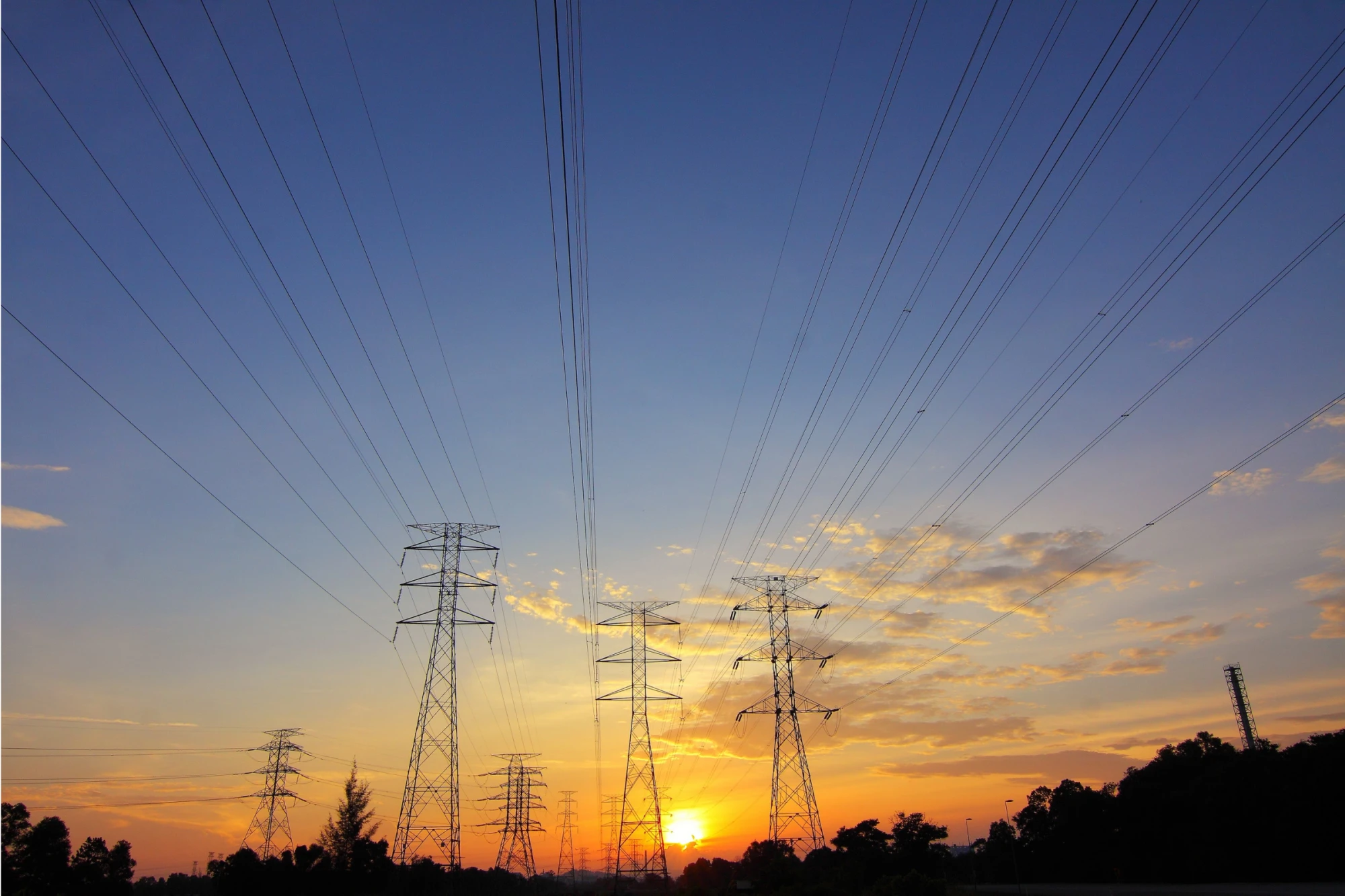
Our Approach to Energy Efficiency
Throughout our facilities, our teams work to identify best practices for energy efficiency that we embed into our business operations — including converting to LED lighting, improving fleet fuel efficiency in our transportation units, optimizing refrigeration and steam operations, covering anaerobic wastewater lagoons for biogas collection, and more. To date, two of our facilities use biogas as a renewable energy source, and 100% of the electricity that our Pilgrim's Europe Pork and Pilgrim's Europe Prepared Foods facilities source is renewable. In 2023, 14.2% of our indirect energy came from renewable sources across our operations.
Pilgrim’s Global decreased total energy use intensity by 6% and fuel use intensity by 8% from 2019 to 2023 — a marked improvement from our process in 2022 (3.8% and 5.6% respectively). Our commitment to reach 60% renewable energy by 2030 will continue to be our focus as we work to reduce energy consumption throughout our operations.
We partnered with local utility providers and third-party energy consultants to identify energy savings opportunities across multiple Pilgrim’s U.S. facilities. This process also included an audit of our routing operations and recommendations for best practices to reduce energy consumption. In 2023, we implemented several projects based on 2022 consultant findings and are currently monitoring and quantifying the reductions as a result. We are continuing to partner with local utility providers and to engage consultants on energy opportunities.
From 2016 to 2023, Pilgrim’s Mexico has seen a nearly 60% reduction in its liquefied petroleum (LP) gas consumption in its incubation department – from 507,587 liters to 207,962 liters. This was a result of several energy efficiency strategies implemented over the years to reduce LP gas consumed for heating, still maintaining temperature requirements through various rooms and areas of the hatcheries. The center consists of six hatcheries with a cumulative loading capacity of nearly six million fertile eggs per week.
Our Approach to Energy Efficiency
Throughout our facilities, our teams work to identify best practices for energy efficiency that we embed into our business operations — including converting to LED lighting, improving fleet fuel efficiency in our transportation units, optimizing refrigeration and steam operations, covering anaerobic wastewater lagoons for biogas collection, and more. To date, two of our facilities use biogas as a renewable energy source, and 100% of the electricity that our Pilgrim's Europe Pork and Pilgrim's Europe Prepared Foods facilities source is renewable. In 2023, 14.2% of our indirect energy came from renewable sources across our operations.
Pilgrim’s Global decreased total energy use intensity by 6% and fuel use intensity by 8% from 2019 to 2023 — a marked improvement from our process in 2022 (3.8% and 5.6% respectively). Our commitment to reach 60% renewable energy by 2030 will continue to be our focus as we work to reduce energy consumption throughout our operations.
We partnered with local utility providers and third-party energy consultants to identify energy savings opportunities across multiple Pilgrim’s U.S. facilities. This process also included an audit of our routing operations and recommendations for best practices to reduce energy consumption. In 2023, we implemented several projects based on 2022 consultant findings and are currently monitoring and quantifying the reductions as a result. We are continuing to partner with local utility providers and to engage consultants on energy opportunities.
From 2016 to 2023, Pilgrim’s Mexico has seen a nearly 60% reduction in its liquefied petroleum (LP) gas consumption in its incubation department – from 507,587 liters to 207,962 liters. This was a result of several energy efficiency strategies implemented over the years to reduce LP gas consumed for heating, still maintaining temperature requirements through various rooms and areas of the hatcheries. The center consists of six hatcheries with a cumulative loading capacity of nearly six million fertile eggs per week.
Our Approach to Energy Efficiency
Throughout our facilities, our teams work to identify best practices for energy efficiency that we embed into our business operations — including converting to LED lighting, improving fleet fuel efficiency in our transportation units, optimizing refrigeration and steam operations, covering anaerobic wastewater lagoons for biogas collection, and more. To date, two of our facilities use biogas as a renewable energy source, and 100% of the electricity that our Pilgrim's Europe Pork and Pilgrim's Europe Prepared Foods facilities source is renewable. In 2023, 14.2% of our indirect energy came from renewable sources across our operations.
Pilgrim’s Global decreased total energy use intensity by 6% and fuel use intensity by 8% from 2019 to 2023 — a marked improvement from our process in 2022 (3.8% and 5.6% respectively). Our commitment to reach 60% renewable energy by 2030 will continue to be our focus as we work to reduce energy consumption throughout our operations.
We partnered with local utility providers and third-party energy consultants to identify energy savings opportunities across multiple Pilgrim’s U.S. facilities. This process also included an audit of our routing operations and recommendations for best practices to reduce energy consumption. In 2023, we implemented several projects based on 2022 consultant findings and are currently monitoring and quantifying the reductions as a result. We are continuing to partner with local utility providers and to engage consultants on energy opportunities.
From 2016 to 2023, Pilgrim’s Mexico has seen a nearly 60% reduction in its liquefied petroleum (LP) gas consumption in its incubation department – from 507,587 liters to 207,962 liters. This was a result of several energy efficiency strategies implemented over the years to reduce LP gas consumed for heating, still maintaining temperature requirements through various rooms and areas of the hatcheries. The center consists of six hatcheries with a cumulative loading capacity of nearly six million fertile eggs per week.

Efficiency by Design
Pilgrim’s Europe’s Chicken business built its Lincolnshire, U.K. poultry farm with sustainability top of mind – intending to reduce Scope 1 and Scope 2 emissions by up to 100%. The facility, named Beech Farm, integrates sustainable practices starting from the farm’s design to its layout. Beech Farm uses technology and other best practices to reduce emissions – including ground source heat pumps to generate heating, heat exchanger systems that reduce overall heat use, and solar technology that can generate 1MW of electricity (working together with lithium battery storage). The latest biosecurity measures are in place to ensure safety and welfare standards for its birds.
As a result of these innovations, Pilgrim’s Europe’s Chicken Beech Farm has seen a 100% reduction in energy-related greenhouse gas (GHG) emissions, representing 900 metric tons of CO2e savings a year. When all systems operate at capacity, this scale can effectively take the farm ‘off-grid.’
This project can serve as a best-in-class example of how to successfully implement a self-sustaining farm. Pilgrim’s Europe plans to share best practices (e.g., knowledge and technical assistance) with its network of poultry producers. This project, coupled with Pilgrim’s Europe’s other Scope 3 initiatives (e.g., “Farm Carbon Calculator” that will track and monitor GHG emissions across its entire farming base in real-time at individual farm level) has the potential to change the game for the industry.
Efficiency by Design
Pilgrim’s Europe’s Chicken business built its Lincolnshire, U.K. poultry farm with sustainability top of mind – intending to reduce Scope 1 and Scope 2 emissions by up to 100%. The facility, named Beech Farm, integrates sustainable practices starting from the farm’s design to its layout. Beech Farm uses technology and other best practices to reduce emissions – including ground source heat pumps to generate heating, heat exchanger systems that reduce overall heat use, and solar technology that can generate 1MW of electricity (working together with lithium battery storage). The latest biosecurity measures are in place to ensure safety and welfare standards for its birds.
As a result of these innovations, Pilgrim’s Europe’s Chicken Beech Farm has seen a 100% reduction in energy-related greenhouse gas (GHG) emissions, representing 900 metric tons of CO2e savings a year. When all systems operate at capacity, this scale can effectively take the farm ‘off-grid.’
This project can serve as a best-in-class example of how to successfully implement a self-sustaining farm. Pilgrim’s Europe plans to share best practices (e.g., knowledge and technical assistance) with its network of poultry producers. This project, coupled with Pilgrim’s Europe’s other Scope 3 initiatives (e.g., “Farm Carbon Calculator” that will track and monitor GHG emissions across its entire farming base in real-time at individual farm level) has the potential to change the game for the industry.
Efficiency by Design
Pilgrim’s Europe’s Chicken business built its Lincolnshire, U.K. poultry farm with sustainability top of mind – intending to reduce Scope 1 and Scope 2 emissions by up to 100%. The facility, named Beech Farm, integrates sustainable practices starting from the farm’s design to its layout. Beech Farm uses technology and other best practices to reduce emissions – including ground source heat pumps to generate heating, heat exchanger systems that reduce overall heat use, and solar technology that can generate 1MW of electricity (working together with lithium battery storage). The latest biosecurity measures are in place to ensure safety and welfare standards for its birds.
As a result of these innovations, Pilgrim’s Europe’s Chicken Beech Farm has seen a 100% reduction in energy-related greenhouse gas (GHG) emissions, representing 900 metric tons of CO2e savings a year. When all systems operate at capacity, this scale can effectively take the farm ‘off-grid.’
This project can serve as a best-in-class example of how to successfully implement a self-sustaining farm. Pilgrim’s Europe plans to share best practices (e.g., knowledge and technical assistance) with its network of poultry producers. This project, coupled with Pilgrim’s Europe’s other Scope 3 initiatives (e.g., “Farm Carbon Calculator” that will track and monitor GHG emissions across its entire farming base in real-time at individual farm level) has the potential to change the game for the industry.
Energy Performance*
Energy Performance*
Energy Performance*
2019 | 2020 | 2021 | 2022 | 2023 | |
Pilgrim's U.S. | 3,508,295,101 | 3,401,305,938 | 3,393,567,822 | 3,432,377,443 | 3,539,977,198 |
Pilgrim's Europe | 1,166,202,011 | 1,108,122,765 | 1,299,600,619 | 1,209,674,105 | 1,101,694,916 |
Pilgrim's Mexico | 859,652,640 | 837,513,179 | 857,721,644 | 735,157,539 | 745,235,161 |
2019 | 2020 | 2021 | 2022 | 2023 | |
Pilgrim's U.S. | 1,129,736,945 | 1,091,467,719 | 1,108,882,715 | 1,109,508,450 | 1,124,278,470 |
Pilgrim's Europe | 336,778,901 | 315,177,245 | 398,759,314 | 379,950,992 | 382,490,052 |
Pilgrim's Mexico | 219,551,171 | 217,158,178 | 220,760,599 | 222,874,796 | 230,894,605 |
*We make every effort to report accurate data. We provide updated data from previous years in cases where improved information is available. Pilgrim’s revisited data collection and as a result, this report includes some improved metrics from past years.
*We make every effort to report accurate data. We provide updated data from previous years in cases where improved information is available. Pilgrim’s revisited data collection and as a result, this report includes some improved metrics from past years.
*We make every effort to report accurate data. We provide updated data from previous years in cases where improved information is available. Pilgrim’s revisited data collection and as a result, this report includes some improved metrics from past years.
Our Stories
Our Stories